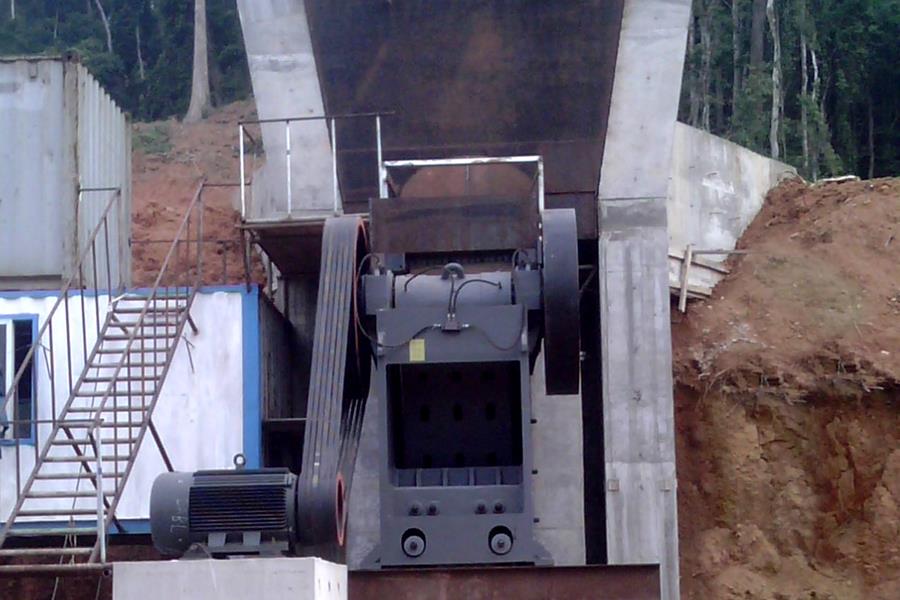
Technology for Improving Bearing Vibration and Noise Reduction
A large number of tests at home and abroad have shown that the processing quality of cages, rings, and steel balls have varying degrees of influence on bearing vibration, among which the processing quality of steel balls has the most obvious impact on bearing vibration, followed by the processing quality of rings, the most important influence Factors are the roundness, waviness, surface roughness, surface bumps, etc. of steel balls and ferrules.
In our case, the most prominent problem of steel ball products is the large dispersion of vibration values and serious surface defects (single point, group point, pit, etc.), although the surface roughness, size, shape, and error are not lower than the level outside the circle, However, the vibration value of the bearing after the assembly is high, and even abnormal sound is generated. The main problem is that the waviness is not controlled (no standard, no suitable test and analysis instrument), and at the same time, it shows that the vibration resistance of the machine tool is poor. There are problems; on the other hand, it is necessary to improve the management level to avoid random quality problems such as bumps, scratches, and burns.
For the ring, the channel waviness and surface roughness are the most serious factors that affect the vibration of the bearing. For example, when the roundness of the inner and outer grooves of small and medium-sized deep groove ball bearings is greater than 2 μm, it will have a significant impact on the vibration of the bearing. It can increase the vibration by more than 4dB, and even produce abnormal sound.
Whether it is a steel ball or a ferrule, the waviness is produced in the grinding process. Although super-finishing can improve the waviness and reduce the roughness, the most fundamental measure is to reduce the waviness during the super-finishing process and avoid randomness There are two main measures for bump injuries:
One is to reduce the vibration of rolling surface grinding and superfinishing, and obtain good surface processing shape accuracy and surface texture quality. The oilstone oscillation system of the fine machine tool has good anti-vibration performance; to increase the grinding speed, 60,000 electric spindles are generally used for grinding 6202 outer raceways abroad, and the grinding speed is above 60m/s, which is generally much lower in China, mainly affected by the spindle and Limitation of main bearing performance. In high-speed grinding, the grinding force is small, the grinding metamorphic layer is thin, it is not easy to burn, and it can improve the machining accuracy and efficiency, which has a great impact on low-noise ball bearings; the dynamic and static stiffness of the spindle and its speed characteristics have great influence on low-noise ball bearings. Grinding vibration has a great influence, the higher the stiffness, the less sensitive the grinding speed is to the change of grinding force, the smaller the vibration of the grinding system; the rigidity of the spindle bearing is improved, and the random dynamic balance technology is adopted to improve the vibration resistance of the grinding spindle sex. The vibration speed of foreign grinding heads (such as Gamfior) is about one-tenth of that of domestic general spindles; it is very important to improve the cutting performance and dressing quality of grinding wheel oilstone. At present, the main problems of grinding wheel oil stones in my country are poor uniformity of structure, which seriously affects the quality of low-noise ball bearing grinding and overprocessing; sufficient cooling to improve filtration accuracy; improvement of feed resolution of fine feeding system and reduction of feed inertia; reasonable grinding and overprocessing Process parameters and processing flow are factors that cannot be ignored. The grinding allowance should be small, and the shape and position tolerances should be strict. The outer diameter of small and medium-sized ball bearings should not be super-finishing, and the coarse and fine grinding superfines should not be separated to ensure good surface quality.
The second is to improve the accuracy of the machining datum surface and reduce the error in the grinding process. The outer diameter and end face are the positioning references in the grinding process. The error reflection of the outer diameter to the groove superprecision is indirectly transmitted through the error reflection of the outer diameter to the groove grinding, and the groove grinding to the groove superprecision. If the workpiece is bumped and damaged during the transfer process, it will be directly reflected on the raceway processing surface, which will affect the vibration of the bearing. Therefore, the following measures must be taken: improve the accuracy of the surface shape of the positioning reference; transfer smoothly during processing, without bumps; At the end, the shape accuracy has not been improved to the final quality requirements, seriously affecting the consistency of processing quality.
From the above analysis, it is not difficult to see that the automatic line mode composed of high-performance and high-stability machine tool system is the most suitable for ultra-processing low-noise ball bearings, which can avoid bumps, reduce transmission errors, eliminate artificial factors, and improve processing efficiency and quality consistency. , Reduce production costs and improve enterprise efficiency.
If you plan to purchase crushing and grinding equipment such as crushers, stone crushers, and mills, please consult the website customer service, 24 hours online.
-
How to reduce the waste caused by the ball mill in operation
-
What should be paid attention to in the routine inspection of the ball mill
-
All machinery must be shut down when repairing sand making equipment