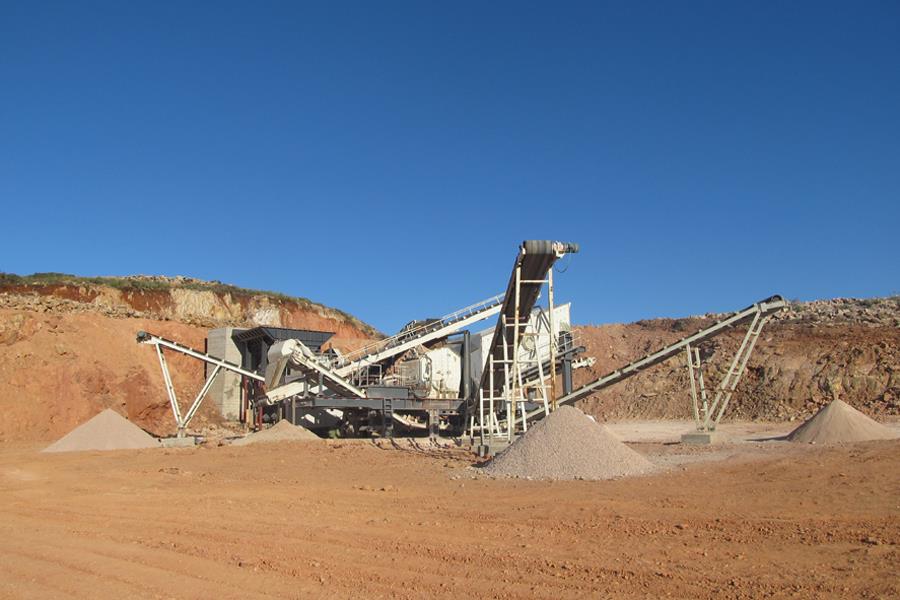
The main reason of cone crusher main shaft fracture and solution measures
Cone crusher has a wide range of applications in mining, metallurgy, chemical industry, coal and other industries. In its working process, the main shaft breakage is a common fault, the fault will seriously affect the normal work of the crusher. Therefore, effective measures should be taken to avoid the occurrence of this fault.
The main factors of cone crusher main shaft fracture:
1. Due to the unique working characteristics of the crusher, the main shaft suffers fatigue damage from frequent mechanical impacts over a long period of time.
2. Excessive feeding, resulting in equipment overload.
3. Ore in the extraction and transportation process, often mixed with some waste metal objects, these objects through the upper end of the tape set electromagnet, due to the weak adsorption capacity of the electromagnet, coupled with manganese-containing steel material metal properties, the electromagnet can not be excluded, resulting in these materials mixed in the ore and slurry into the crusher, resulting in frequent over-ferrous iron, which causes frequent impacts on the spindle and other components. So that the main shaft to produce fatigue damage, is the main reason for the main shaft fracture.
Preventive measures:
1. When carrying out maintenance work, the on-site maintenance personnel should recycle the waste parts replaced by the cone crusher and put them into the designated location, and it is strictly prohibited to discard all kinds of metal waste into the ore at will.
2. When overhauling the equipment, the maintenance personnel of the ore dressing workshop should strictly abide by the operation regulations, and avoid leaving the maintenance tools and sundries in the equipment.
3. Through purchasing and relying on its own technical force, update or remodel the existing metal detector to improve the ability of metal detector to detect and eliminate metal.
4. The operator who guards the feeding tape of the crusher should strengthen the sense of responsibility, increase the inspection of the materials, and pick out the foreign materials in time.
5. Jaw crusher operators should be in place for timely inspections, and should deal with and report on abnormalities such as current and sound to prevent accidents from expanding.
6. Regularly use ultrasonic and other instruments to detect injuries on the main shaft and other stressed parts, in order to understand the actual condition of the current jaw crusher equipment.
7. Strengthen the training of operators of each section, try to improve the practical operation level of operators, strengthen the maintenance of equipment, and make timely repair of equipment in order to ensure that the equipment is in good technical condition.
8. For the main shaft, carcass and other key equipment parts that can affect the production of the whole system, do a good job of purchasing spare parts in stock, so as not to cause the whole system to shut down after the emergence of special circumstances.
We are a professional manufacturer of crushing and grinding equipment, welcome to click on customer service to learn about equipment prices, production cases and other detailed information, 24 hours online free consultation.