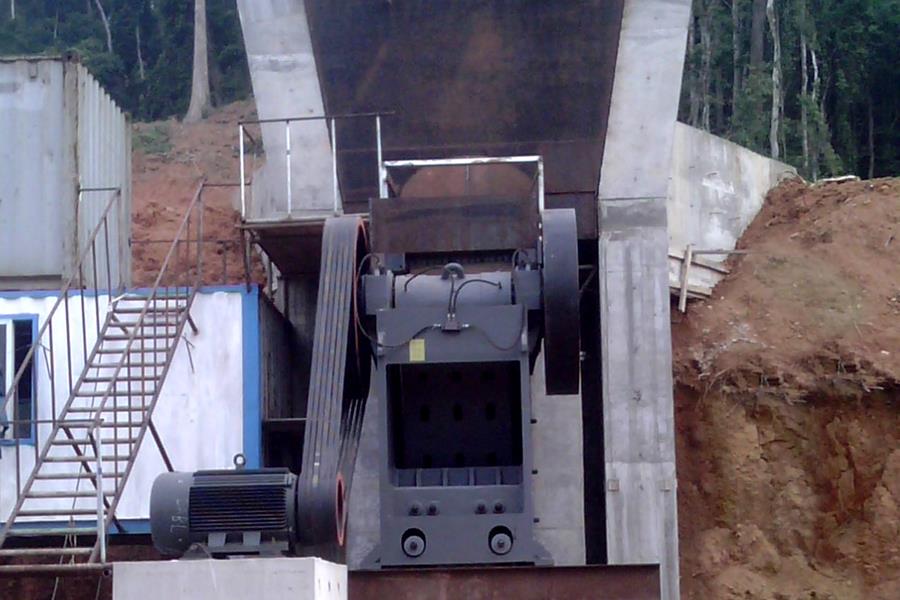
Process design of granite crushing and screening plant
Granite belongs to a class of materials which is more difficult to crush, but it is usually slightly easier to crush than basalt. This is because granite has high hardness but has certain brittleness. Therefore, the design of the crushing process can be relatively flexible, if the customer has the advantage of the market price, you can use the two-stage crushing process scheme. However, from the long-term production point of view, the three-stage crushing process is still the method that can effectively reduce the production cost.
If the customer's market does not require high grain size of the finished stone, a two-stage jaw crushing solution can be used for production. This configuration is the lowest investment, the easiest to maintain and the most economical of all options. However, the disadvantage of this solution is that the grain size of the stone is relatively poor and the proportion of needle-shaped material is high. The stone is not very competitive in the market, because high-grade construction requires stone with excellent granularity. In order to improve the granularity of the stone (polycube), a jaw crusher plus impact crusher process configuration can be used. This configuration has a higher investment cost than the two-stage jaw crusher mentioned above, and produces a very good granularity of stone. However, since granite is a difficult material to crush, the wear and tear of the impact crusher is relatively high, and the increase in production cost for long-term production is considerable. Because of the brittle nature of granite, this configuration is also an acceptable solution.
If the granularity of the product is excellent and the production cost is low, then we need to add a laminated crusher between the jaw and impact crusher, such as a fine jaw crusher or a cone crusher. This configuration allows the main crushing work to be done by the first and second crushers (laminated crushing), and finally the impact crusher to do the whole crushing. Such a configuration process can greatly reduce the counter material formed after screening. If the proportion of counter material in a production line is too high, it will make the last crusher add too much repetitive crushing work, and accordingly make the wear and tear of wear parts will be greatly increased. The two-stage laminated crushing and third-stage impact crushing configuration increases the investment cost, but reduces the production cost significantly. The advantages are self-evident.
The specific process configuration needs to be analyzed according to the actual situation on site, welcome to visit and exchange. You can also consult our website customer service first to understand, 24 hours online, to provide free consulting services.
-
Stone crusher can process the type of stone and particle size range
-
How much does the whole set of crushing production line equipment cost