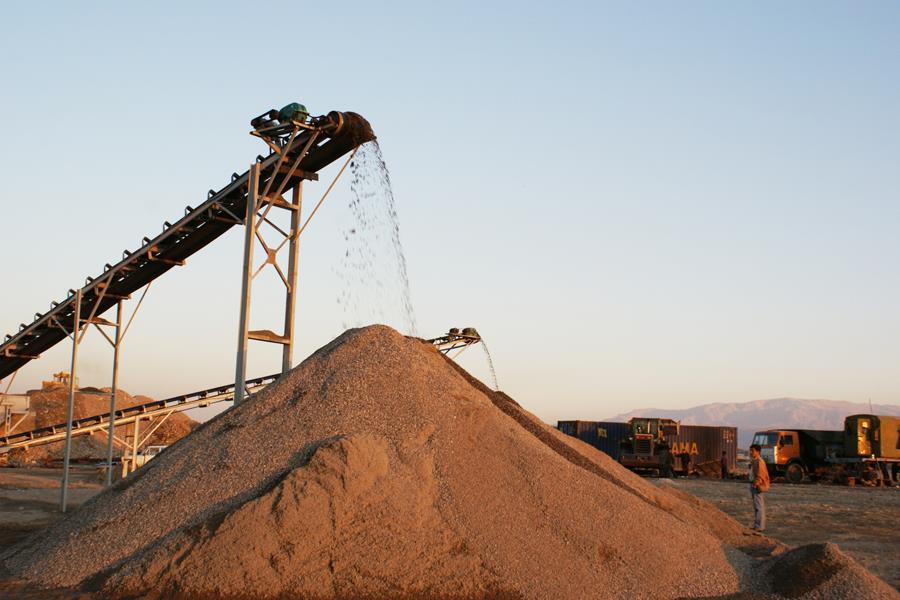
Adjustment of crusher drive unit
In order to adapt the crusher to the requirements of product size and crusher over iron, the center distance of the two rolls have to change, and the two crushing rolls have to rotate synchronously. In order to adapt to this situation early production of crushers mostly use a single motor long tooth gear drive.
The disadvantages of this type of drive are: the center distance displacement is small, the gears are not easy to manufacture, and the gears are severely worn, even playing teeth. Adopting double motor drive, that is, each motor drives a roller by belt or reducer, which can remove a pair of long-tooth gear drive. However, two speed reducers must be equipped, and the cost is increased again. In addition, as the movable bearing needs to move, the belt transmission makes its tensioning force change; if the reducer drive, there must be installed universal joints, in order to allow the shaft to move horizontally with the rolls without affecting the normal work of the crusher. For fine break crusher, using a single electric drive, a pair of car tires can be used instead of long tooth gear drive. In effect, this replaces the gear-tooth drive with a pair of tires in a friction drive. This type of drive is used in several countries on top of crushers.
In the case of double stick crusher, the transmission system is motor, pinion gear, large gear, fixed roller, fixed roller tire, and movable roller driving the movable roller to rotate. Since the tire is flexible, even if the movable roller moves slightly, the tire of the fixed roller can transmit the movement to the tire of the movable roller, and the noise during transmission is relatively small.
The grading crusher generally adopts double motors, hydraulic coupling and gear reducer to drive the toothed rolls. The main advantages of this transmission method are: high transmission power, suitable for large processing capacity and high intensity crushing conditions, easy to achieve lower speed of crushing rolls. The disadvantages are: relatively more transmission links, more failure points, high maintenance volume, high maintenance costs; poor adjustability of the two roller spacing.
For the case of large changes in the center distance, a single motor with time-varying axis distance equal speed ratio transmission mechanism can be used. This combination transmission not only realizes the time-varying axis distance equal speed ratio transmission can allow the center distance change to reach the center distance in normal working condition, but also can realize the equal strength design with small design space is my problem, thus greatly improving the service life of the transmission mechanism.
If you are interested in our company and our products, welcome to visit our company or our local office, you can also send an email or leave your contact information, our staff will contact you as soon as possible to provide you with product information and application knowledge, so that you can finally not only get high quality new equipment but also get attentive service.