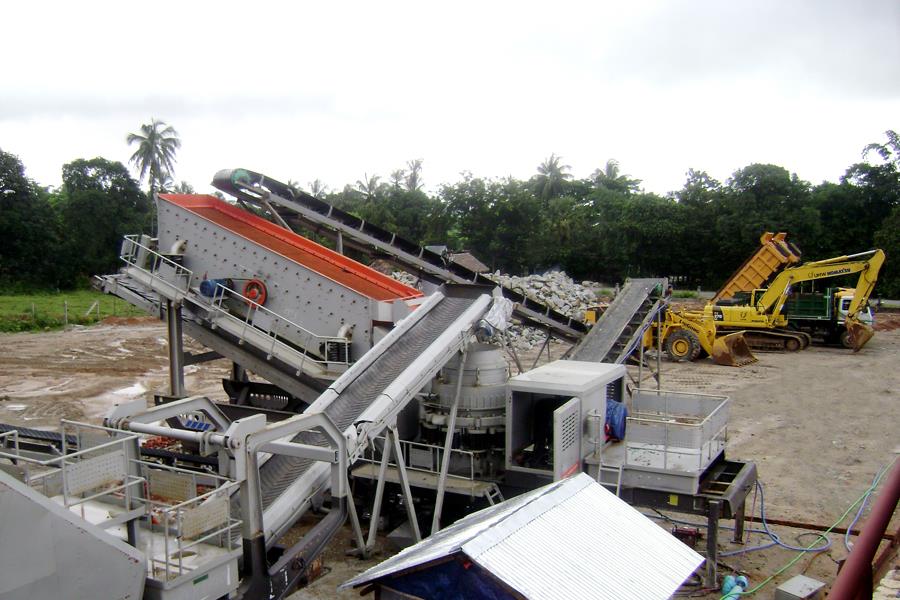
How many valves in the grinding production line and their roles respectively
To ask how many valves in the milling production line, we all know that the grinding equipment consists of hundreds of components, the valve is just one of them, the number and type of valves are clearly defined and the role of small and inconspicuous, but also an indispensable part of the production line, today we will recognize the composition of the milling equipment of the various types of valves and their roles are what?
Strictly speaking, the main valves of the milling production line has three, for the downcomer valve, the main wind valve, the remaining wind valve, in addition there are four observation doors, an access door, they are located in the lower end of the cyclone collector, the return air duct, the bag duster pipeline, the snail shell, the host casing, each valve according to its role in characterizing the design of the structure is different, here's a look at their respective roles in which?
1. Downcomer valve: that is, the lock powder, the main role of closed lock powder, we all know that the material to reach the cyclone collector at the material and the airflow began to separate, the material was collected under the action of gravity to the collector, the airflow will be back to the wind pipe conveyor to the blower to start the next round of transportation, the role of the downcomer valve is very critical at this time, not out of the material should be kept completely closed, otherwise there will be a leakage of the mouth of the downcomer dust increased Otherwise, there will be air leakage and dust increase in the lower feeding port, which will reduce the efficiency of milling production.
2. Main air door: the main air door in the return air duct, by controlling the size of the diameter of the pipe ventilation to control the entire milling production line air volume, the smaller the valve opening state, the weaker the air volume in the transmission pipeline, and vice versa, the stronger the excess fan with the use of the Raymond Mill until the grinding to achieve a better production results.
3. The remaining wind door: the remaining wind valve is installed in the pipeline connected with the bag filter, mainly affecting the feed port air volume, thus affecting the air volume of the conveying pipeline, the valve should be in a state of readiness to start 1/3 open state, if the feed port has a spraying condition in the gradual opening of the feed port until the powder does not come out of the powder until the door, the remaining wind door and the main air door is very similar to the role from the structure to the role of the door.
4. Observation door: observation door evenly distributed in the mill host shell around, from the name of the name is the role of observation, at the same time when the host feed blockage can then be 4 observation door will be pulled out of the material, troubleshooting, which is also regarded as evenly dispersed around the design of the snail shell is the most important one of the application.
5. Maintenance door: in the middle of the mill host shell, is also the most conspicuous valve, when the host internal failure problems can be repaired from this door, convenient and time-saving.
Although the above variety of valves are simple and inconspicuous, but each of them serves an important role in the milling production line, regardless of whether the valve open state is normal or not due to damage can not work will affect the whole machine production and processing, in addition to a variety of valves with the continuous improvement of milling technology in the role of the design is also advancing with the times, such as the discharging device door from the original manual control has gradually changed into an electronically controlled, automation performance to strengthen energy saving and labor costs. Labor costs, there are four small observers inside the smooth design, no eddy current, reducing the resistance of air transmission, etc.. The above valve failure rate is low, less mobilization, more than once adjusted to a better state can be without much thought, but if the opening state caused by the mill other failure problems must pay attention to the inspection and adjustment.
Valve state is not right may cause failure problems as follows:
1. The milling equipment does not produce powder or powder less low yield.
2. Serious powder spraying at the feeding port.
3. The finished powder is too coarse or too fine.
4. Observe the phenomenon of air leakage and powder leakage at the door.
But encountered the above similar problems is to be sure not to forget the various types of valves to check the working status. Mill quality is not only reflected in the grinding rollers grinding ring and other major wearing parts of the material and workmanship, it should be a comprehensive reflection of the mill machine, of course, including the above valve design and manufacturing process, grinding production line machine quality enhancement, mill prices will increase, so as a mine mill manufacturers in the material selection, manufacturing process should be noted, and the use of customers may pay attention to the daily correct operation, repair and maintenance! Attention.
Click on the website customer service to learn more, 24 hours online, free consultation.
-
Detailed explanation of the internal structure of the jaw crusher and selling point advantages
-
Configuration scheme of 20 tons per hour 300 mesh lime powder
-
Mill motor model selection and daily work need to pay attention to what issues
-
Is it better to selfsupply or outsource the desulfurization agent of the power plant